Strict Quality Control & Inspection
“Every product undergoes strict quality checks — from raw materials to final packaging. Our on-site QC team follows international AQL standards to ensure there’s no compromise on quality.”
“Inspected to protect your brand reputation.
We believe you quality isn’t just a box to tick — it’s a non-negotiable promise. We understand that your brand’s reputation depends on every stitch, seam, and surface. That’s why we’ve built a rigorous, multi-layered quality control system that covers every step of the production journey — from fabric sourcing and cutting to final inspection and packaging.
We work with certified factories in Bangladesh that follow global compliance protocols and our own internal QC team provides on-site monitoring and independent checks, using internationally recognized AQL (Acceptable Quality Limit) standards.
Our Quality Control Framework
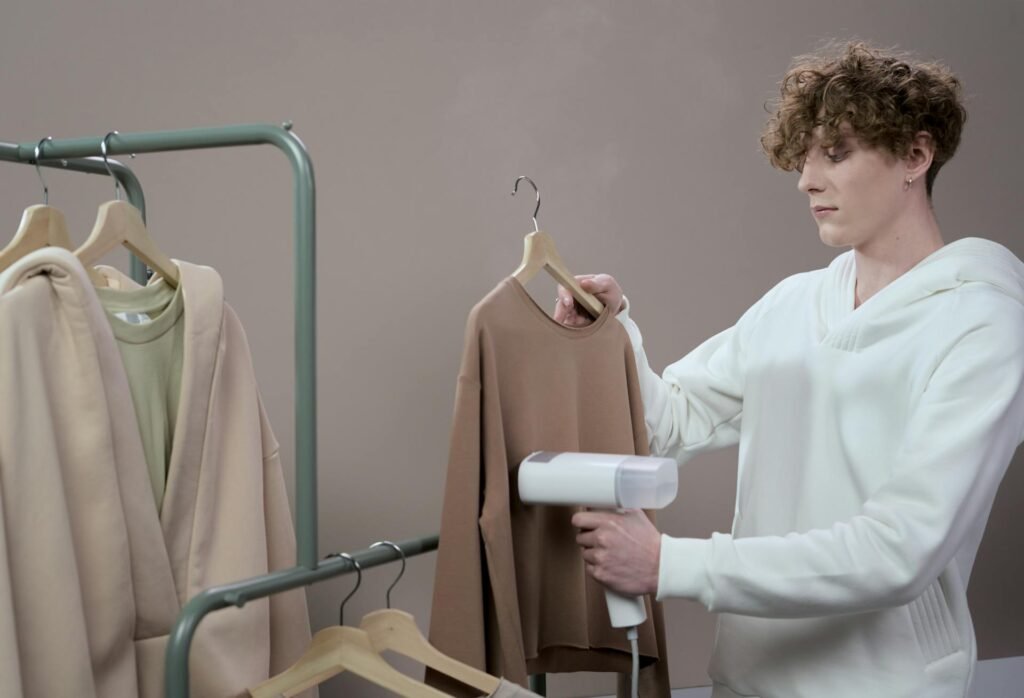